The Rise of CNC Precision Machining Manufacturers in Metal Fabrication
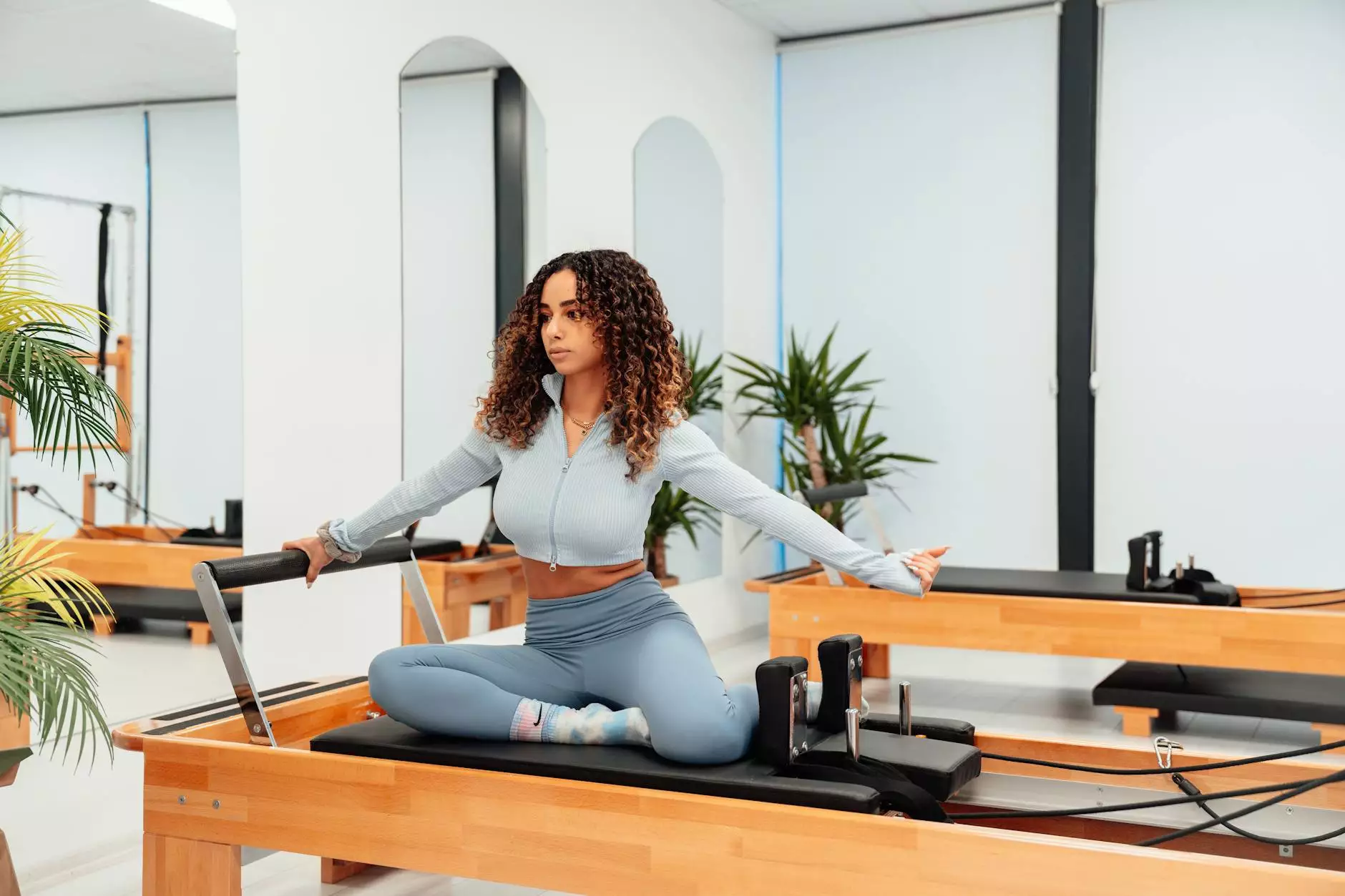
The landscape of modern manufacturing has undergone a dramatic transformation, particularly in the field of metal fabrication. The emergence of CNC precision machining manufacturers has turned traditional methods on their head, introducing a new era defined by accuracy, efficiency, and versatility. This article explores the pivotal role that these manufacturers play in the industry, highlighting their importance, technologies, and the future of metal fabrication.
Understanding CNC Precision Machining
At its core, CNC (Computer Numerical Control) machining refers to the automated control of machining tools such as drills, mills, and lathes by a computer. This technology allows for the precise fabrication of parts and components, effectively eliminating the inconsistencies that are often present in manual machining processes.
How CNC Machining Works
The CNC process begins with a detailed design of the part to be manufactured, typically created in CAD (Computer-Aided Design) software. This design is then converted into code using CAM (Computer-Aided Manufacturing) software, which instructs the CNC machine on how to operate. Key steps include:
- Design: Create a 3D model of the component using CAD software.
- Programming: Generate G-code that defines the toolpaths for the CNC machine.
- Setup: Equip the machine with the necessary tools and materials.
- Machining: Execute the program to cut and shape the material as per specifications.
- Finishing: Apply finishing touches such as sanding, coating, or polishing as needed.
The Importance of CNC Precision Machining Manufacturers
As industries evolve towards increased globalization and competition, the demand for high-quality precision parts has surged. Here’s why CNC precision machining manufacturers play an indispensable role in the metal fabrication sector:
1. Enhanced Precision and Accuracy
One of the foremost advantages of CNC precision machining is its unparalleled accuracy. Unlike manual machining, CNC machines can reproduce the same part thousands of times with minimal variance. This reliability is crucial for industries such as aerospace, automotive, and medical, where tolerances can be extremely tight.
2. Increased Efficiency and Productivity
CNC machines are capable of running continuously, 24/7, which significantly boosts productivity. The automated nature of CNC machining also minimizes human error, further enhancing efficiency. Consequently, businesses can reduce production times, meet tighter deadlines, and lower operational costs.
3. Versatility in Material Usage
CNC machining supports a variety of materials, including various metals, plastics, and composites. This versatility allows precision machining manufacturers to cater to a wide array of industries, offering bespoke solutions tailored to specific requirements.
4. Cost-Effectiveness
While the initial investment in CNC technology can be substantial, the long-term savings are considerable. Reduced waste, fewer defects, and the ability to produce complex parts without extensive labor contribute to overall cost efficiency.
Technological Innovations in CNC Machining
The field of CNC machining is continuously evolving, with advancements in technology enhancing manufacturing capabilities. Some notable innovations include:
1. 5-Axis Machining
5-axis CNC machining allows for complex geometries to be produced in a single setup. This technology improves efficiency by reducing the need for multiple setups and tooling. It is especially beneficial for aerospace and defense applications, where precise and intricate designs are mandatory.
2. Automation and Robotics
The integration of robotics in CNC machining streamlines production processes. Automated robotics can handle tasks such as part loading and unloading, quality inspection, and even secondary operations, maximizing operational efficiency and minimizing human intervention.
3. Additive Manufacturing Integration
The fusion of CNC machining and additive manufacturing (3D printing) enables hybrid manufacturing solutions. This synergy allows manufacturers to create complex geometries and lightweight structures that were previously unattainable, revolutionizing how parts are produced.
Choosing the Right CNC Precision Machining Manufacturer
When selecting a CNC precision machining manufacturer, businesses must consider several critical factors to ensure they partner with a capable and competent provider:
1. Experience and Expertise
Look for manufacturers with a proven track record in the specific industry you operate in. Their experience can provide insights into best practices and innovative solutions tailored to your needs.
2. Certification and Compliance
Ensure that the manufacturer adheres to industry standards and certifications such as ISO 9001. Compliance with these standards indicates a commitment to quality and excellence.
3. Technology and Equipment
Inquire about the types of CNC machines and technologies used by the manufacturer. Advanced equipment can lead to improved precision and efficiency in the machining process.
4. Customer Support and Communication
Effective communication is essential for successful collaboration. Choose a manufacturer that prioritizes transparency and offers robust customer support to address any concerns promptly.
5. Reviews and Testimonials
Research customer reviews and testimonials to gauge the satisfaction level of previous clients. Positive feedback can be an excellent indicator of reliability and quality.
Future Trends in CNC Precision Machining
The future of CNC precision machining is promising, driven by technological advancements and market demands. Here are some trends to watch:
1. Integration of IoT and Smart Manufacturing
The Internet of Things (IoT) is poised to transform CNC machining by enabling smarter manufacturing processes. Real-time monitoring and data analytics can lead to better decision-making, predictive maintenance, and enhanced operational efficiency.
2. Sustainability in Manufacturing
As environmental concerns grow, manufacturers are increasingly focusing on sustainable practices. This includes minimizing waste, using recyclable materials, and adopting energy-efficient technologies in CNC machining.
3. Customization and Personalization
The demand for customized products is rising. CNC precision machining manufacturers are expected to invest in more flexible and adaptive systems that can quickly switch between various products without significant downtime.
4. Advanced Materials and Innovations
The introduction of advanced materials, such as composites and high-performance alloys, will challenge CNC machining manufacturers to adapt their processes. Innovations in material science will open new avenues for product development.
Conclusion
In conclusion, the role of CNC precision machining manufacturers in the metal fabrication industry is integral and evolving. Their ability to produce high-quality, precise parts efficiently and reliably positions them as invaluable partners in today’s competitive landscape. As technology advances, these manufacturers will continue to innovate, ensuring they remain at the forefront of the manufacturing revolution. Embracing CNC machining technology is not just a choice but a strategic imperative for businesses looking to thrive in an increasingly demanding global market.
For more information on leading CNC precision machining solutions, visit DeepMould.net.