Duplex Stainless Steel vs 316: A Comprehensive Comparison
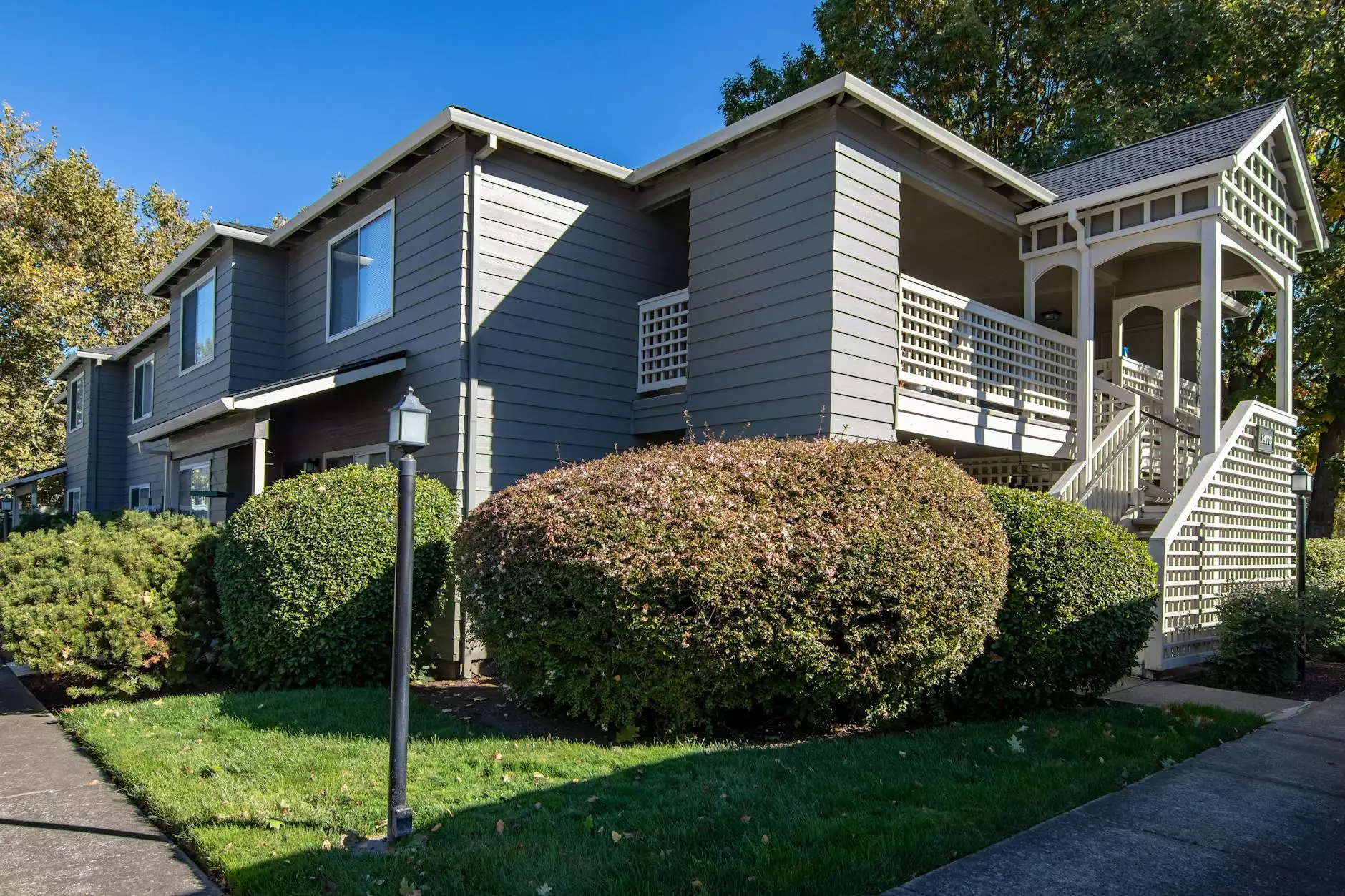
In the world of stainless steel, two materials frequently compared for their properties and applications are Duplex Stainless Steel and 316 Stainless Steel. Both of these alloys possess unique characteristics that make them suitable for various applications, but understanding their differences is crucial for making informed decisions in manufacturing and construction.
Understanding Duplex Stainless Steel
Duplex Stainless Steel is a family of stainless steels that combine the best properties of both ferritic and austenitic stainless steels. Typically composed of around 22% chromium, 5% nickel, and 3% molybdenum, this steel has a mixed microstructure of about 50% austenite and 50% ferrite. This distinct combination provides enhanced strength and improved resistance to corrosion compared to standard austenitic stainless steels.
Key Properties of Duplex Stainless Steel
- High Strength: Duplex steels generally have higher tensile strength, making them suitable for high-stress applications.
- Corrosion Resistance: Excellent resistance to chloride-induced stress corrosion cracking, pitting, and crevice corrosion.
- Cost-Effectiveness: Their superior strength allows for thinner sections to be used, potentially reducing overall costs in construction.
- Weldability: While they can be welded, special techniques may be required to avoid embrittlement during the welding process.
Understanding 316 Stainless Steel
316 Stainless Steel, on the other hand, is an austenitic alloy, widely recognized for its excellent corrosion resistance and overall versatility. It typically contains 16% chromium, 10% nickel, and 2% molybdenum. This composition grants it superior resistance to pitting caused by chlorides, making it a preferred choice in marine environments and other corrosive settings.
Key Properties of 316 Stainless Steel
- Corrosion Resistance: Outstanding resistance to corrosive media, especially in chloride environments.
- Weldability: Excellent for welding applications, and it retains its corrosion resistance even after welding.
- Formability: Highly machinable and easy to form into various shapes and components.
- Temperature Resistance: Holds up well in high-temperature applications up to approximately 925°C.
Comparing Duplex Stainless Steel and 316 Stainless Steel
When it comes to the comparison of Duplex Stainless Steel vs 316, both materials have their strengths and weaknesses, which can lead to different applications depending on the environment and requirements. Here’s a detailed comparison:
Strength and Durability
Duplex stainless steel excels in strength, often achieving up to double the yield strength of 316 stainless steel. This high strength can be particularly beneficial in applications that face varying loads and environmental stresses, allowing for lighter structures that do not compromise on strength.
Corrosion Resistance
Both alloys offer substantial corrosion resistance; however, Duplex stainless steel is specifically designed to resist pitting and chloride-induced corrosion even better than 316 in certain environments. This property makes Duplex more advantageous in chemical processing and oil and gas extraction, where the presence of aggressive materials is common.
Weldability
While 316 stainless steel is easier to weld, Duplex stainless steel requires specific welding procedures to maintain its desirable properties. Welding Duplex can lead to undesired phases if not done correctly, highlighting the importance of technical expertise in fabrication.
Price and Cost Efficiency
Duplex stainless steel tends to be more expensive than 316 stainless steel due to its superior alloying elements and processing. However, the overall cost-effectiveness of Duplex steels should not be overlooked. The higher tensile strength allows for thinner sections, which can lead to overall material savings in large-scale applications.
Applications in Various Industries
Both Duplex Stainless Steel and 316 Stainless Steel are widely utilized across various industries, depending on their unique properties. Here’s how they are applied:
Duplex Stainless Steel Applications
- Oil and Gas Industry: Used in pipelines, valves, and other components due to its strength and corrosion resistance.
- Marine Applications: Ideal for shipbuilding, oil rigs, and offshore applications due to its ability to resist saline environments.
- Chemical Processing: Employed in storage tanks and processing equipment where aggressive chemicals are present.
316 Stainless Steel Applications
- Food and Beverage Industry: Used extensively in equipment where hygiene is critical due to its excellent corrosion resistance and easy cleanability.
- Medical Equipment: Utilized in surgical tools, implants, and devices that require sterility and reliability.
- Architecture: Common in building facades, handrails, and other structures exposed to the elements.
Choosing the Right Alloy
When deciding between Duplex Stainless Steel vs 316, it is essential to consider the specific requirements of your project:
- Environmental Conditions: Evaluate the corrosive environment where the material will be utilized.
- Load Requirements: Assess the mechanical stress that the materials will need to withstand.
- Cost Considerations: Determine overall budget constraints while weighing the benefits of each material.
- Fabrication Needs: Consider the complexity of welding and forming processes required for each alloy.
Conclusion
In summary, both Duplex Stainless Steel and 316 Stainless Steel provide unique strengths tailored to different industry needs. While Duplex offers superior strength and corrosion resistance, 316 remains favored for its ease of fabrication and versatility. Understanding the differences and advantages of each material is critical for making informed choices in manufacturing and construction projects.
For more information on stainless steel and its various applications, contact us at Tech Tubes, where we specialize in high-quality tube fittings, ferrule fittings, flanges, and other fittings to suit your needs.